Albany MEDICAL CENTER Cogeneration Plant, Albany, New York
Facing significant expansion, both immediate and in the future, Albany Medical Center explored their options for meeting the additional power consumption levels necessitated by growth.
CHP Program Manager: Cogen Power Technologies
Design-Builder: Bette & Cring
With a $330 Million expansion project underway, Albany Medical Center’s (AMC) energy consumption is increasing dramatically. To meet this demand, Cogen developed a solution that gives them firmer control over costs; reduced carbon footprint; and opportunities for growth. Cogen provided a single source Design- Build contract and assisted in securing a $2 Million NYSERDA grant.
One of the biggest challenges was building the two-story, 23,000 SF plant on an extremely difficult site. The hilly, densely-urban site with an operating daycare center and steam pipes crossing overhead, required phasing work around active uses and constructing the plant one half at a time.
The new $23 Million cogeneration plant will work in conjunction with the utility to supply electricity and heat, and provide back-up service during outages. It includes a 4.6 MW Gas Turbine, a 60,000 pph Heat Recovery Steam Generator (HRSG), a gas compressor, two 500-ton electric centrifugal chillers, a control room, shop areas, and an office, with room to double capacity (can house a second 4.6 MW turbine and HRSG pair, plus up to 1500 tons of absorption chillers).
During power outages, the plant will run on a standalone basis and allow the hospital to continue operations. Cogen developed a state-of-the-art “Load Management System” to control the supply of electricity during crises and sheds loads during outages so that the system is not overloaded.
With a fully-collaborative process, Cogen was able to deliver a project that more than meets expectations. Construction of the building was completed under schedule and $360,000 under budget. AMC’s carbon emissions will be reduced by 20,000 tons per year – equivalent of taking 3,234 cars off the road. AMC will experience significant cost savings – project buyback is 7-9 years, while the life of the turbine extends to more than 20 years.
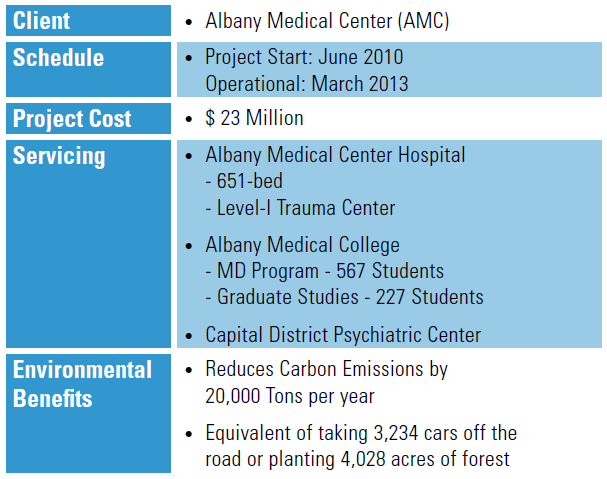
The project site selected tested the creativity and problem-solving skills of both the designers and the construction crew.
- Dense urban site with limited space
- Site had existing daycare center and steam pipes crossing overhead on piers
- Hilly site surrounded by active driveways, no laydown area,
- Phased work around active uses
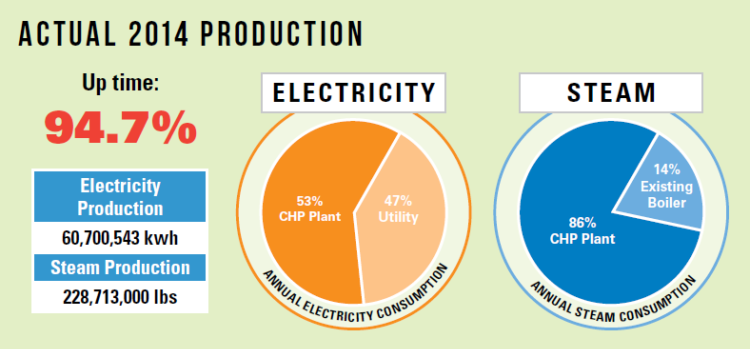

CHILLERS
(2) 530 TONS, R134-A REFRIGERANT

STEAM CONDENSATE TANK
& D/A (DE-AERATOR) TANK

BLACKSTART GENERATOR
750 KW DIESEL GENERATOR
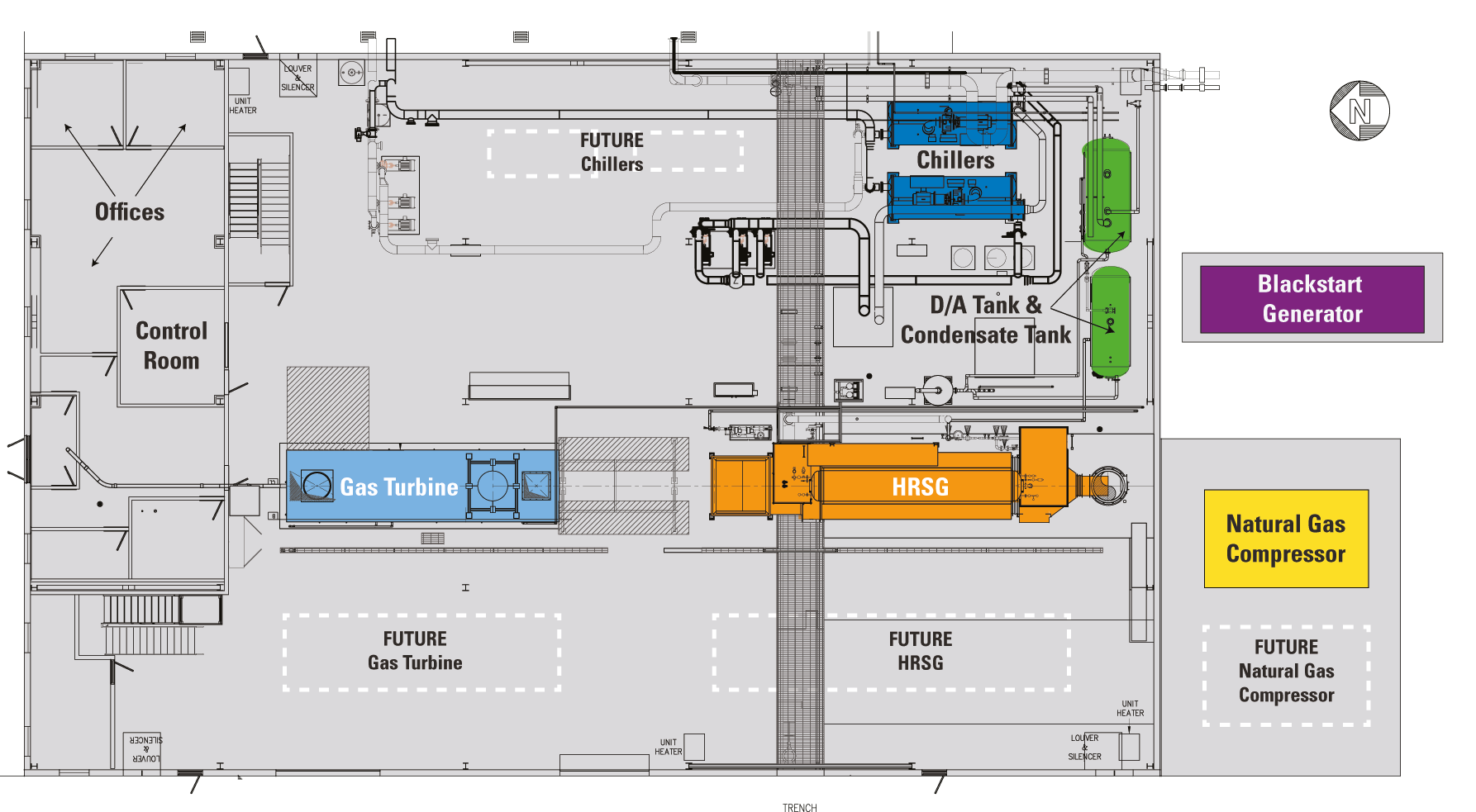

CHILLERS
(2) 530 TONS, R134-A REFRIGERANT
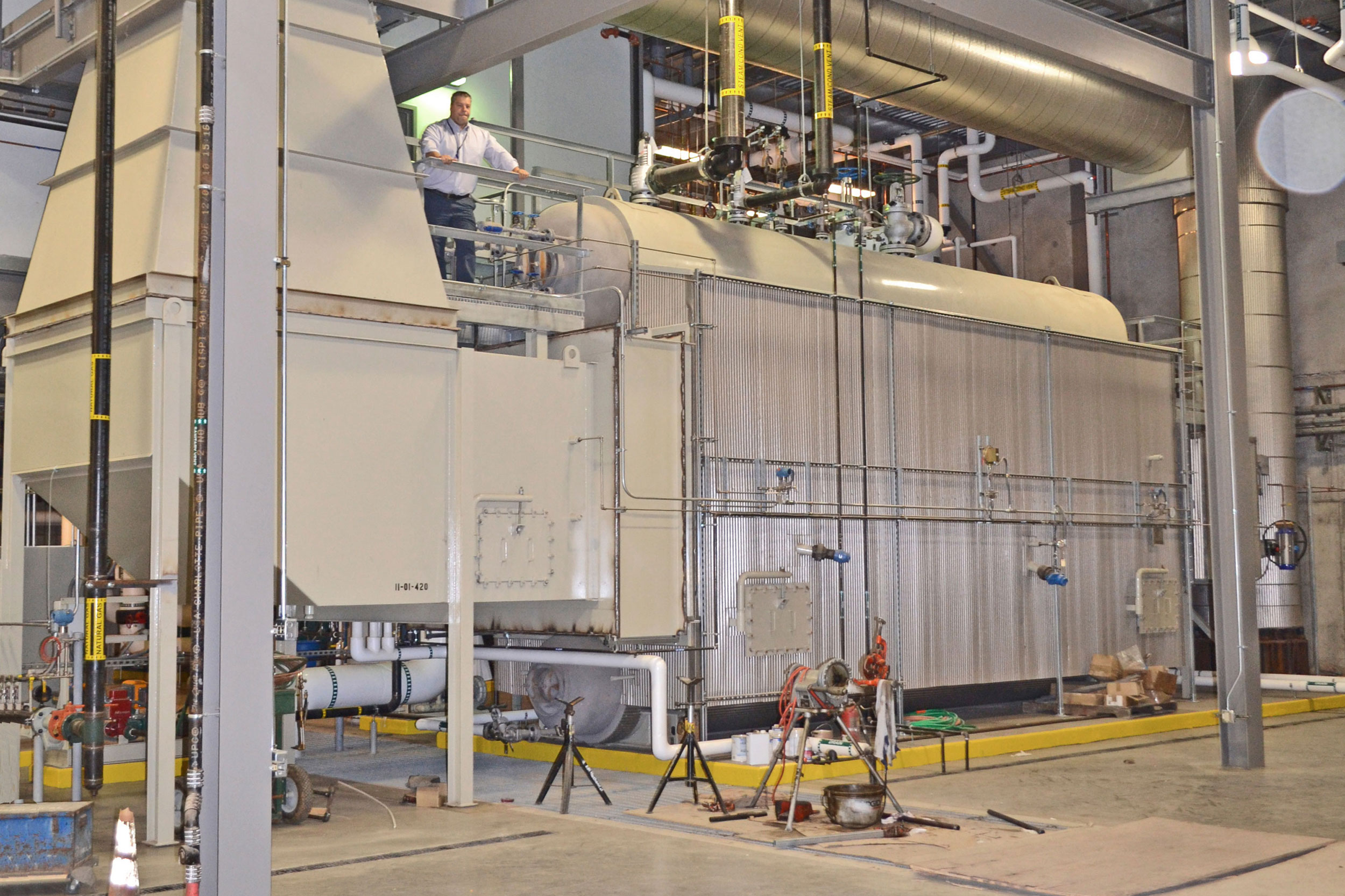
STEAM CONDENSATE TANK
& D/A (DE-AERATOR) TANK

BLACKSTART GENERATOR
750 KW DIESEL GENERATOR